The buffer area is the sterile zone in pharmaceutical manufacturing. Generally compounding area in sterile pharmaceutical preparation facility is known as the buffer area. The buffer area is always ISO 7 area (class 10,000) or better air quality.
Buffer areas always contain positive pressure to avoid the entrance of particle and microbial contaminants and differential pressure should be maintained between 10-20 pascals. HVAC system helps to maintain the pressure and the air quality of the area. Buffer areas should be surrounded by ISO 7 (class 10,000) or ISO 8 (class 1,00,000) areas.
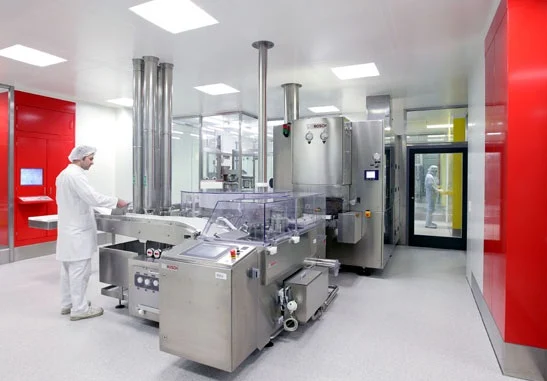
According to USP 〈797〉Pharmaceutical Compounding—Sterile Preparations, unwanted objects (computers, printers, carts, cabinets etc.) that are not essential for compounding, cannot be placed in the buffer areas. Only devices used in compounding should be placed in buffer areas. This area should be accessible to only the personnel trained and authorized for compounding activities and cleaning.
Buffer areas or clean rooms should not contain any source of water. Therefore, sinks or drains should not be there in buffer areas. An eye washer can be installed for any emergency during manufacturing and that should be cleaned and disinfected properly.
If the objects are placed in the buffer area, the area should be validated in the presence of those objects showing that these do not affect the quality of the area. The environmental monitoring should be done for viable and non-viable particles and results should meet the area quality. The area must be re-qualified after the addition of a new device or object that is not essential for compounding in the buffer area.
The quality of air in the buffer areas must be validated at least once in six months and all the validation tests including the air flow pattern should be done properly.
No comments:
Post a Comment
Please don't spam. Comments having links would not be published.